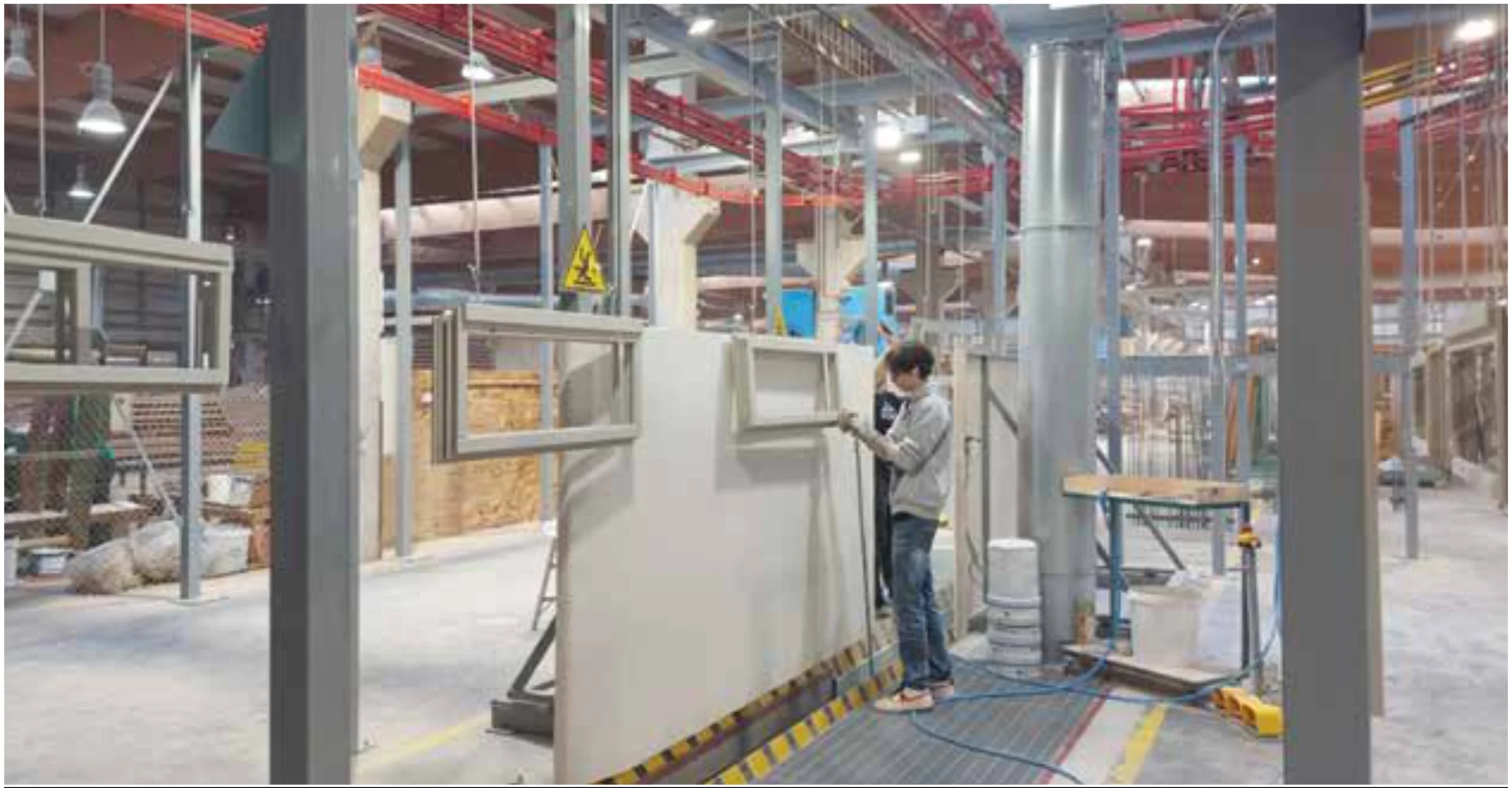
Inwestycja w nowoczesny zakład lakierniczy zaprocentuje innowacyjną produkcją
Firma CDM, renomowany polski producent okien i drzwi, nawiązała współpracę z liderem w dziedzinie projektowania systemów lakierniczych – włoską firmą Finiture. Pośrednikiem tego partnerstwa jest firma ITA, która od lat skutecznie wprowadza na polski rynek m.in. najnowsze technologie Finiture. Efektem tej współpracy jest zaawansowany zakład lakierniczy, który podnosi standardy jakości, efektywności i zrównoważonego rozwoju w branży stolarki budowlanej.
Tradycja spotyka innowację
Założona w 2001 roku firma CDM łączy tradycyjne rzemiosło z nowoczesnymi technologiami. Specjalizując się w produkcji stolarki drewnianej oraz drewniano-aluminiowej, firma wyróżnia się zdolnością realizacji nietypowych projektów oraz spersonalizowanych rozwiązań, które odpowiadają na indywidualne potrzeby klientów. Współpraca z dostawcami najwyższej jakości materiałów – zarówno polskimi, jak i zagranicznymi – pozwala CDM oferować produkty, które charakteryzują się wyjątkową trwałością i niezawodnością.
Nowoczesny zakład lakierniczy: pełna automatyzacja i precyzja
Zakład lakierniczy zaprojektowany przez Finiture to prawdziwa rewolucja w procesach wykończeniowych. Nowoczesne linie lakiernicze stawiają na innowacyjne technologie, które nie tylko poprawiają efektywność pracy, ale także znacząco redukują zużycie energii cieplnej i emisję CO2. W najnowszym projekcie zastosowano rozwiązania pozwalające na odzyskiwanie energii w kluczowych obszarach, takich jak kabiny lakiernicze i tunele suszarnicze, a także wdrożono system suszenia LDP (Low Dew Point), który wprowadza nową jakość w procesie suszenia farb wodorozcieńczalnych. Kluczowym elementem systemu jest linia transportowa wyposażona w podwójną szynę i punkty mocowania, które umożliwiają stabilne i bezpieczne przemieszczanie okien oraz drzwi przez wszystkie etapy lakierowania. Dzięki modułowej konstrukcji system zapewnia efektywne zarządzanie procesami i ciągły przepływ produkcji. W centralnym punkcie zakładu znajduje się kabina lakiernicza z pełną recyrkulacją powietrza. Tworzy ona kontrolowane środowisko, w którym możliwe jest precyzyjne i równomierne nakładanie lakieru. Proces ten odbywa się za pomocą zaawansowanego robota RAS. Wyposażony w antropomorficzne ramię, robot ten zapewnia nie tylko stałą jakość wykończeń, ale także znaczną redukcję zużycia lakierów, co ogranicza ilość odpadów i przekłada się na niższe koszty produkcji. Robot jest wspierany przez system automatycznej zmiany kolorów i czyszczenia dysz, który pozwala na szybką adaptację linii do różnorodnych
potrzeb produkcyjnych, minimalizując czas przestojów. W zakładzie znajduje się także kabina przeznaczona do ręcznego nakładania specjalnych produktów. Dzięki zaawansowanym systemom regulacji wilgotności i temperatury możliwe jest precyzyjne dostosowanie warunków do specyficznych wymagań każdego projektu. Linia lakiernicza obejmuje dwie kabiny o łącznym przepływie powietrza wynoszącym 40 000 m³/h. W tradycyjnych rozwiązaniach całość zużytego powietrza byłaby wydalana na zewnątrz, a jego uzupełnienie wymagałoby ogrzewania powietrza zewnętrznego do temperatury wewnętrznej. W projekcie zastosowano system rekuperacji, który pozwala na odzyskanie i ponowne wykorzystanie 80% powietrza, co odpowiada aż 32 000 m³/h. Dzięki temu rozwiązaniu ilość powietrza wymagającego ogrzania jest znacząco mniejsza, co przekłada się na oszczędność energii cieplnej proporcjonalną do różnicy temperatur między powietrzem wewnętrznym a zewnętrznym. Dodatkowo, wentylatory wprowadzające powietrze z zewnątrz są mniej obciążone, co oznacza oszczędność energii elektrycznej rzędu 4,9 kW.
Suszenie i szlifowanie w nowej odsłonie
Po zakończeniu lakierowania elementy są transportowane do strefy suszenia wyposażonej w innowacyjną technologię LDP. System ten wykorzystuje zaawansowaną kontrolę elektroniczną, która w czasie rzeczywistym reguluje temperaturę i wilgotność, dostosowując się do warunków środowiskowych.
W efekcie proces suszenia jest nie tylko bardziej efektywny, ale także znacznie oszczędniejszy pod względem
zużycia energii w porównaniu z tradycyjnymi technologiami. Tradycyjne tunele suszarnicze wykorzystują
gorące powietrze do eliminacji wilgoci z farb, co wiąże się z dużym zużyciem energii. Nowatorski system LDP zmienia to podejście, opierając się na osuszaniu powietrza. Dzięki zmniejszeniu wilgotności, proces suszenia staje się bardziej wydajny, co pozwala ograniczyć wykorzystanie energii cieplnej bez wydłużania czasu
pracy. System LDP bazuje na zaawansowanej jednostce uzdatniania powietrza, która osusza i ogrzewa powietrze, wykorzystując cykl chłodniczy i technologię pomp ciepła. Dodatkowe wsparcie
zapewnia wężownica gorącej wody, jednak jej zużycie energii cieplnej jest minimalne w porównaniu z tradycyjnymi rozwiązaniami. Kolejnym istotnym elementem linii jest obszar szlifowania, który został zaprojektowany z myślą o maksymalnej ergonomii i wydajności. Wyposażono go w system odciągów podłogowych oraz regulowane wsporniki, które ułatwiają precyzyjną obróbkę elementów.
Nowoczesne zarządzanie produkcją
Całością proces.w zarządza zaawansowany system nadzoru, kt.ry umożliwiające łatwe i intuicyjne sterowanie linią. Dzięki temu operatorzy mogą szybko dostosować parametry pracy
do bieżących potrzeb, co zwiększa efektywność i minimalizuje ryzyko błędów.
Ekologia i innowacja w centrum uwagi
Nowoczesny zakład lakierniczy CDM to nie tylko wzrost jakości i wydajności produkcji, ale także odpowiedź na rosnące wymagania związane z ochroną środowiska. Technologie zastosowane przez Finiture, takie jak recyrkulacja powietrza czy optymalizacja zużycia energii, pozwalają na znaczną redukcję emisji i odpad.w. Dzięki temu firma CDM może realizować swoje cele biznesowe w zgodzie z zasadami zr.wnoważonego rozwoju.